Coi Rubber utilizes the rubber compression molding process to produce a range of precision rubber molded components. The benefits of rubber compression molding are realized in a number of areas. From low to medium volume applications. You can also find them for some specialty high volume components. Products produced from Coi’s proprietary compression molding rubber process can be designed to be high precision.
Compression Molding Rubber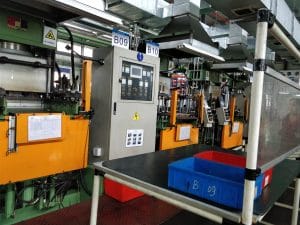
- Perfect for large “bulky” parts and expensive, exotic compounds
- We feature a 72″ x 72″ Press
- 10′ x 42″ Press
- 10′ x 30″ Press
- 54″ x 60″ Press and several smaller presses
Advantages of Compression Molding Rubber
- Tooling can be less complex and lower cost to construct
- Lower percentage material runner scrape vs. traditional injection or transfer molding
- Process is suitable from most elastomers and cure systems
Disadvantages of Compression Molding vs. other rubber molding methods
- Labor for preforming material can add cost
- Cycle times may be longer
Compression Molding: A Low Cost Option
Compression molding rubber is often used to form large or intricate parts and produces very little wasted material. It is one of the lowest-cost molding methods especially when you work with Coi Rubber because we produce your parts in-house from start to finish. If you need large or intricate rubber parts, we often recommend a compression molding solution. This is a highly efficient option, and we can handle every step of the manufacturing process, from start to finish. You send us the print, and we’ll take care of the rest. We will create your mold (or use your supplied mold), determine the proper rubber formulation to meet your specifications, mix the rubber, preform it and manufacture your parts.
Custom Molded Rubber
As a manufacturer of high precision components and assemblies, FDA Class 1, 2 and 3 products, Coi Rubber Products specializes in finding solutions to tough applications which require the molding and assembly of close tolerance components. We offer a wide range of technical services and production capabilities for producing close tolerance injection molded plastic components, assemblies and sub-assemblies. Our specialty processes and services include:
- High performance plastics such as PEEK, Torlon®, Aurum® PI and more.
- Custom Seals and Shapes
- Insert Molding in Thermoplastics, Rubber and Silicone
- Two shot molding
- LSR Molding
- Rotary Seal Rings and Thrust Washers
- Rubber to TPE Conversions
- Metal to Plastic Conversions
- Bonding for plastic to metal, plastic to rubber and plastic to plastic
- Over molding
- Hotplate, rotational and ultrasonic welding
- Adhesive bonding, hot stamping and machining
- Product testing, assembly and packaging
- Unified project management
Rubber Transfer Molding Process
This process is similar to compression molding. The materials will flow from the sprue. They will reach its cavity from heating up a POT system. From a comparison to injection on some liquids, the transfer process will act in a similar fashion.
Compression Molding Rubber & Injection Molding Process
Injection molding of liquid silicone rubber (LSR) is a process to produce pliable, durable parts in high volume. Liquid silicone rubber is a high purity platinum cured silicone with low compression set, great stability and ability to resist extreme temperatures of heat and cold ideally suitable for production of parts, where high quality is a must.
Our in-house rubber formulation and molding facilities can meet our customers’ most precise requirements for customized precision rubber components used in the Automotive, Consumer Electronics and Mobile industries. We have a completely automated mixing facility from the third floor down with full automation and quality control. Coi Rubber offers Rubber Compression and Injection Molding services and is equipped with a wide range of molding machines with clamping forces ranging from 30 to <650 tons. Our highly skilled engineers and technicians work on our computerized injection molding machines to ensure that each molded part meets the product specifications of our customers. These are complemented with various secondary processes including ultrasonic welding, laser marking and robotic spray painting. Our capabilities include:
- Design and fabrication of molding tools (up to 850 tons)
- Injection molding machines (30 to 650 tons)
- Molding of precision engineering parts, including high-speed, electric, vertical, and double shot molding
- Ultrasonic welding
- Heat staking
- Laser marking
- Robotic spray painting and assembly
To gain a better understanding of the compression molding processes, materials and technical considerations involved in the design and manufacture of custom-molded rubber and plastic parts contact us today!