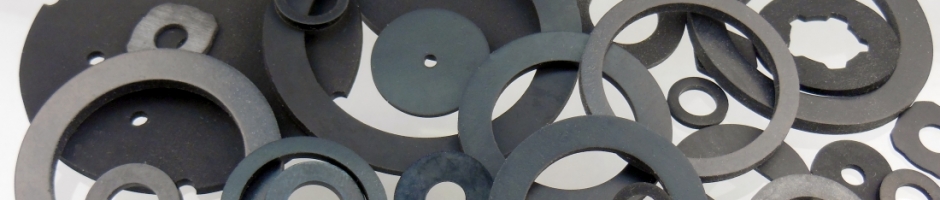
Neoprene vs Natural Rubber in Applications
Neoprene vs natural rubber
Neoprene vs natural rubber is a topic that often appears when comparing two types of rubber. NBR is more popular compared to natural rubber when it comes to gaskets because of its unique characteristics. Neoprene is also found to be common in other applications such as wetsuits, laptop sleeves, and wrist braces. Furthermore, neoprene can provide resistance to oil and grease which is an advantage that neoprene has over natural rubber. Neoprene played a critical role during WW2 because of the limited access to natural rubber. Despite the limited access to natural rubber, militaries were able to still produce vehicles and war machines using neoprene as gaskets and seals. Neoprene provided more suitable characteristics for specific applications in the automotive industry compared to natural rubber.
NBR vs Natural Rubber
The main characteristics that allowed Neoprene to shine over natural were their resistances to oil and grease. These characteristics alone allowed neoprene to excel over natural rubber in critical automotive applications, because natural rubber does not provide resistance to oil and grease as well as Neoprene. Neoprene rubber is also known to have a better temperature tolerance making it a critical synthetic rubber during WW2. This allowed neoprene to be placed near engines compared to natural rubber which could not withstand temperatures of 200°F and above.
Natural rubber would remain unstable at extreme temperatures. Using natural rubber will result in a shorter lifespan for the part. Neoprene also has good compressibility making it an efficient material for insulation and keeping liquids contained. If you are looking to manufacture automotive parts, you should consider if your application calls for the use of Neoprene over natural rubber. Neoprene can survive in outdoor conditions longer compared to natural rubber because of its resistant to ozone and oxidation. This allows Neoprene to not be worn out and cracked when exposed to an outside environment.
The biggest disadvantage of Neoprene, however, is the relatively higher cost of the material. Another concern of Neoprene that may affect performance in a few applications is the material’s poor resistance to strong acids. However, this concern would be unlikely to affect most usages in automotive applications, as the main acid that most rubber might encounter is weak acid from the rain. Despite its higher pricing of Neoprene vs natural rubber, Neoprene is shown to be a major player in the automotive industry with its unique characteristics. These characteristics allowed Neoprene to achieve success in the industry when it outshined natural rubber in the 1920s.
About Coi Rubber Products
Coi Rubber Products, Inc. is a custom manufacturer of molded rubber and plastic components. Coi Rubber has over 28 years of experience in Engineering, Design, Compounding, Prototyping, and Production of molded rubber and plastics. Our capabilities include custom compounding, injection molding, compression molding, transfer molding, extrusions, rubber-to-metal bonding, insert over-molding, and more. We provide large scale production and engineering support to the Automotive, Industrial, Agriculture, Appliance, HVAC industries, and many more. Coi Rubber is IATF 16949:2016 and MBE certified.
Get a quote for your project: sales@coirubber.com
Visit us at: www.coirubber.com
Have a question? Please fill out the form below to receive information regarding your inquiry. You may also give us a call at (626) 965-9966.
Error: Contact form not found.